June 6, 2022
Changing Product Design Paradigms Define Post-COVID Manufacturing
By Paul Sweeney
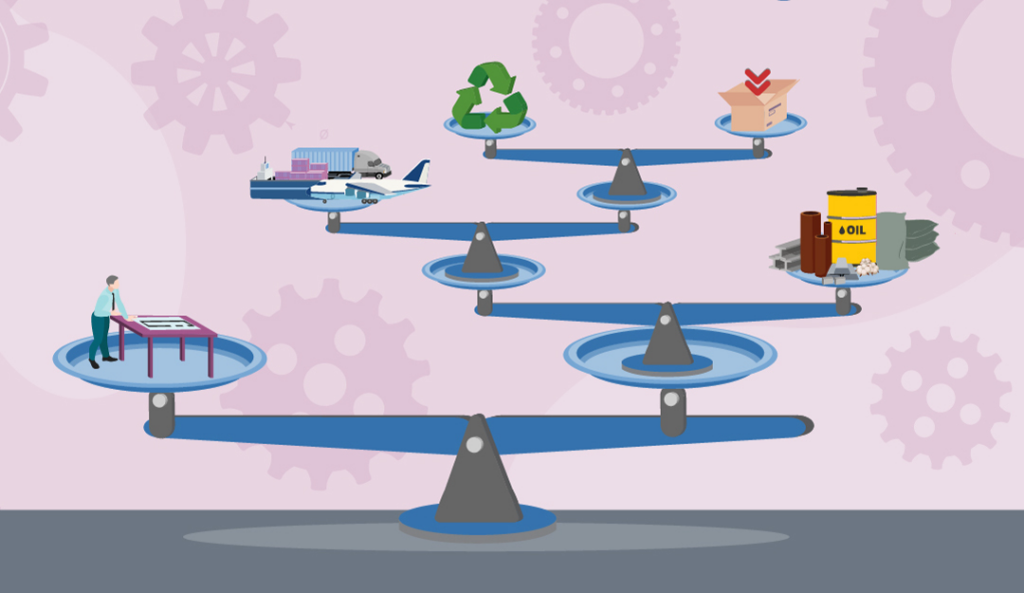
Product development and lifecycle are adversely affected by today’s global supply chain situation in ways many professionals have never experienced before. The electronic device industry encounters sporadic supply shortages from time to time, but rarely do the shortages encompass chips, modules, and passive components all at once – right across the sector.
Today’s upset is unique: it’s not driven by a reduction of demand, but rather by a sudden constriction of the ability to meet that demand, ostensibly as a fallout from the COVID19 pandemic. The outcome is a combination of staffing difficulties alongside the decision of some OEMs to “hoard” components.
In historic terms, current conditions are:
- Extreme
- Short
- Sharp
Production of many sophisticated products – like automobiles, for example – has been halted due to lack of supply of some rather basic electronic parts. Working around those shortages in production has managed to relieve some of that strain, but manufacturers are still facing substantial premiums over agreed pricing for many specialized parts they require.
“Design for Supply” Becoming More Important to Companies Worldwide
Product development and go-to-market strategy rely on components being available on the manufacturer’s shop floor at precisely the right times. To mitigate supply-side risks, designers are now looking to a new paradigm: Design for supply. This represents a decision to embark on designs which deliberately are not reliant on single-sourced components and which use generic parts wherever possible.
While this approach has great potential, it hasn’t been adopted universally. Many organizations are still somewhat in shock: those closer to their supply chains have anticipated outcomes more nimbly and pre-procured inventory or negotiated guarantees of supply. Some organizations, like PCH, now design for supply from the outset.
From the manufacturer’s perspective, some high-end parts that would have enjoyed popularity in high-volume applications have missed out on growth opportunities as a result of the pivot, as products view component selection with this new perspective. This represents an opportunities for global supply chain risk management.
Product companies must stipulate to their design partners that risk analysis is essential from the start and throughout the product development and manufacturing lifecycle. Where risk is moderate or high from the start, a dual-path strategy must be available, offering a “Plan B” in case of further disruption to essential components.
SMBs Must Innovate to Work Around Supply Shortages
Much attention has been given to Apple’s ability to maintain and even expand its smartphone business in the midst of global semiconductor shortages. Through their high degree of vertical integration and their unique market position combined with strong purchasing power, they are much less exposed than virtually all other players.
Without the size, scale, and vertical integration of Apple, SMBs should be very selective about their choice of partners. Working with a company like PCH enables you to benefit from established supply chain partnerships that span many different market segments and programs, providing aggregated economies of scale for each client.
The challenge of small and mid-sized companies in need of greater influence and purchasing power with semiconductor manufacturers is compounded by constrained travel, which has made it more difficult to develop partnerships, inspect potential suppliers, and rebuild or restructure supply chains. PCH stands out for its 25+ year history building supply chain in China. PCH’s deep links in China and integration with international supply chains provide a strong basis for small to mid-sized U.S. and European companies to weather supply chain shocks.
The Biggest Emerging Opportunities in Design for Sustainability
Environmental and sustainability is a high priority for most companies these days. Many companies start their sustainability journey with product packaging, largely because it’s visible and very tangible to them and to consumers. It also represents a very significant amount of waste.
Broadening the scope from packaging to the products has been a slower process for most companies, who have found that to be a more complex challenge.
That this is the case is due to a number of reasons, including: organizational inertial in reacting to relatively new market needs, challenges in carrying out environmental impact assessments of product during product development and in developing suitable options and alternatives. At PCH, we’re committed to help our clients with these challenges, and our team and partners have the goal to offer multiple sustainability options per product to clients, providing lifecycle assessments of environmental impact of component and materials choices.
At the same time, legislation is being enacted in the U.S. and worldwide around the right to repair. This has the potential to drive waste reduction, but products must be designed for reuse and refurbishment. Lifecycle analysis is definitely a growing area, one that PCH hopes to leverage for clients in the future.
Lifecycle Analysis Will Be Essential to Meeting Environmental Impact Goals
Lifecycle analysis is the key to approaching these above opportunities in a systematic way. It is not simply a matter of replacing polycarbonate with a sustainable material and going to market; without a rigorous lifecycle-based approach, activities which appear to offer sustainability gains could actually add to carbon footprint over a product’s lifecycle, rather than offsetting it!
Thus, sustainable product design must be approached through in a holistic manner. Each component in a product affects the others, and so changes should be evaluated at system level. A new material selection may cut down initial waste, but reduce time in usage mode or require complex disposal at end-of-life. All these factors must be taken into account:
- How the product is made
- How the product is used
- The full product lifecycle
- How end-of-life is managed
Clients and the Environment Benefit from PCH’s Evolving Expertise
As a first mover in Design for Sustainability, PCH is positioned to pioneer and build capabilities for sustainable design that are so far unique. A truthful lifecycle analysis for electronic products has always been challenging – today, that goal has become the Holy Grail for product companies.
PCH clients have long had the opportunity to integrate with our MRP systems so they can get reports on demand from us. With access to comprehensive product sustainability lifecycle analyses, it is our goal to provide our clients with the supply chain intelligence to make informed product sustainability decisions at every step. Ultimately, that means a seamless “Design for Sustainability” review in the midst of any design process, defining multiple options for product realization.
Paul Sweeney is the VP of Product Development at the PCH International. He has more than 20 years of experience in design and development of medical electronics, aerospace and consumer electronics products. Paul holds a PhD in biomedical engineering.